Ship propellers, also known as ship’s wings or “baling-baling” in Indonesian, are essential components of a ship’s propulsion system.

The manufacturing process of these propellers involves a series of meticulous and intricate steps that require advanced technology and skilled craftsmanship. In this article, we will take a closer look at the fascinating process that takes place in the factories to make these important parts of a ship.
The first step in the manufacturing process of ship propellers is the design phase. Architects and naval engineers collaborate to develop the most efficient and effective propeller design for a particular ship.
Factors such as vessel type, size, speed requirements, and operating conditions are taken into account during this phase.
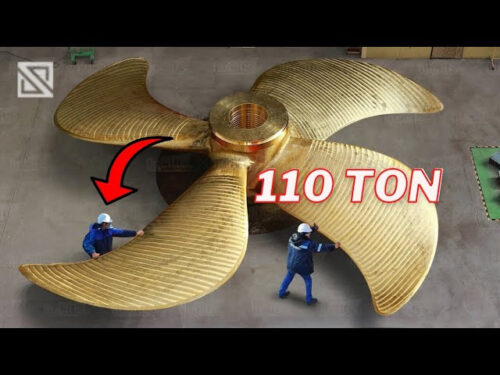
Once the design is finalized, the manufacturing process begins with the selection of the right raw materials. High-quality marine metals, such as copper or stainless steel, are commonly used due to their excellent strength and resistance to corrosion in marine environments.
The next step involves casting the propeller blades. This is usually done through a process called investment casting, also known as the lost wax method. A wax model of the propeller is created and covered with several layers of ceramic. The ceramic-coated wax model is then heated to remove the wax, leaving a hollow ceramic mold.
The molten metal is then poured into the ceramic mold, filling the void and forming a propeller shape. After the metal hardens, the ceramic mold breaks, exposing the raw casting of the propeller blade.
The rough casting then undergoes a series of machining processes to refine its shape and size. This includes removing excess metal, smoothing surfaces, and achieving precise blade profiles.
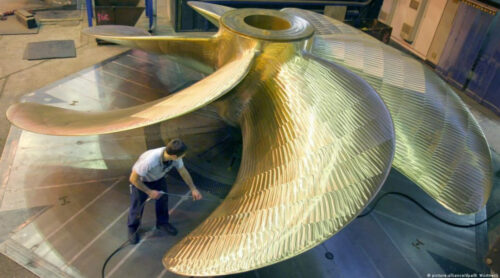
Advanced computer-controlled machinery, such as CNC (Computer Numerical Control) machines, are often used during this stage to ensure accuracy and consistency.
After the machining process, the propellers undergo meticulous quality control and inspection. This involves checking for dimensional accuracy, surface finish, balance, and overall integrity.
Any imperfections or deviations from specifications are addressed and remedied before moving on to the next stage.
In the final step, the propeller blades are polished to achieve a smooth and glossy surface. They are then carefully assembled into a hub, connecting the propellers to the ship’s propulsion system.
The bearing is designed to withstand the forces and stresses applied to the propeller during operation, ensuring it is securely mounted.